LIBRARY
Effects of Encapsulant Properties on the Thermo-Mechanical Reliability of Double-Side Cooled Power Modules for Traction Inverters
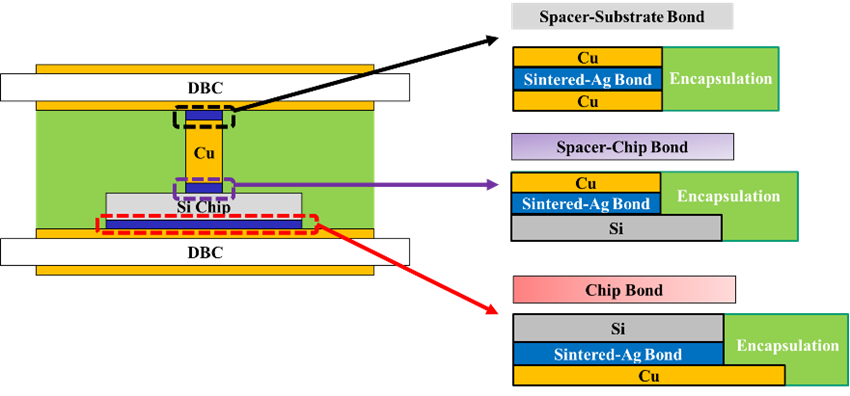
Fig. 1 illustrates the cross-section of a typical DSC module package with all the bonded interfaces: the spacer-substrate bond, the spacer-chip bond, and the chip bond or die attach. The package model resembles the configuration of commercial DSC packages. All the bonds are made by silver sintering, as it is the emerging technology for bonding in power modules. For the thermo-mechanical analysis, the package was subjected to a JESD22-A104-B temperature-cycling test, and the plastic strain and SED per cycle were generated for each bonded interface inside the module.
Fig. 2 is a plot of the effects of encapsulants" elastic modulus and CTE on the plastic strain in the die attach per cycle. The range of each property corresponds to that found in commercial epoxies. The plot shows that both properties affect the bond's plastic deformation; i.e., the higher the elastic modulus or lower the CTE, the lower the plastic strain. Lower plastic deformation generally means less bond fatigue, implying a more reliable bond layer. Similar results were also obtained for the rest of the sintered-silver bond layers, showcasing that the thermo-mechanical reliability of the bonded interfaces in a DSC power module can be strongly affected by the elastic modulus and CTE of the encapsulant.
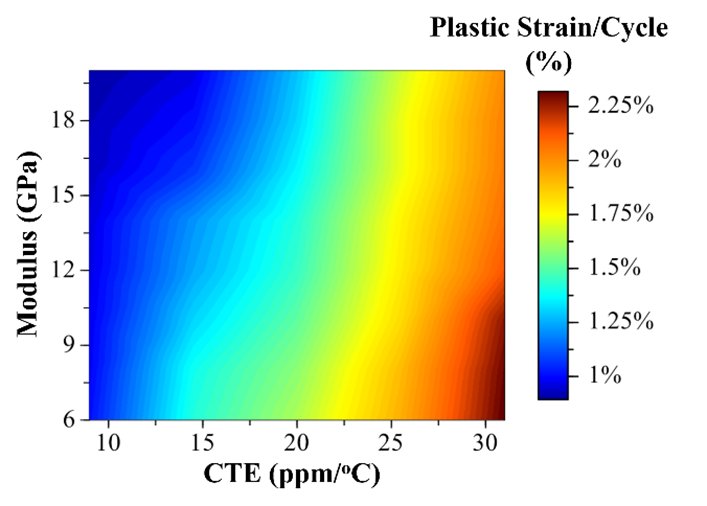