LIBRARY
Electro-Thermal Device-Package Co-Design for Ultra-Wide Bandgap Gallium Oxide Power Devices
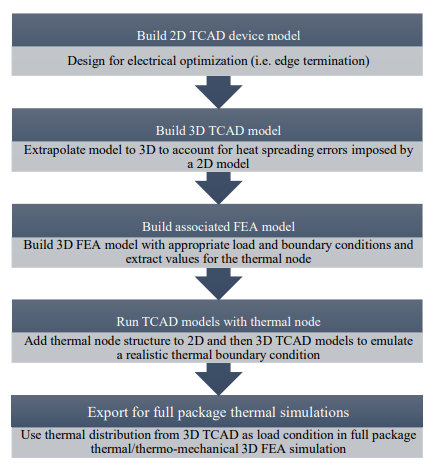
In this work, several modeling methods are explored for an electrothermal device package co-design. The first method selected was a 3D finite element analysis (FEA) multiphysics simulation, which is widely used due to its low computational demands and ability to model not only the heat interactions between material interfaces but also a convection coefficient at the boundary. However, the micro-/nano-scale device structures, lattice-based heating, and thermally dependent electrical parameters are not all modeled. The 2D and 3D physics-based technology computer-aided design (TCAD) models account for these physics effects, but the high computational power required due to the large difference in length scales between the electrically active regions (e.g., nanometer-sized edge termination structures and drift regions) and the thermal diffusion regions (e.g., millimeter-sized packaging structures) as well as the involved physics-based solution method limits their use when package components need to be considered. In addition, TCAD does not have the ability to model a convection coefficient; instead it is limited to conductive heat transfer. These approaches were compared, and it was ascertained that a combination of FEA and TCAD models, detailed in Fig. 1., was warranted for an accurate and efficient electrothermal co-design.
This allows for analysis of the relationship between device structures and the resulting junction temperature and thermal distribution. As a test case, the device thickness, area, and anode diameter were varied to evaluate their impact on thermal performance. TABLE I summarizes the effectiveness of the different device structure modifications that were explored. They are compared to the baseline case, which has a junction temperature of 344°C.
This work outlines and evaluates an electro-thermal device/package co-design model. This process can be utilized for the efficient and accurate modeling of Ga2O3 devices including any hot spots caused by self-heating that would guide the package requirements and design, as well as the impacts of this heating on the electrical performance.
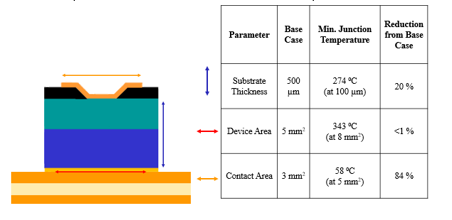