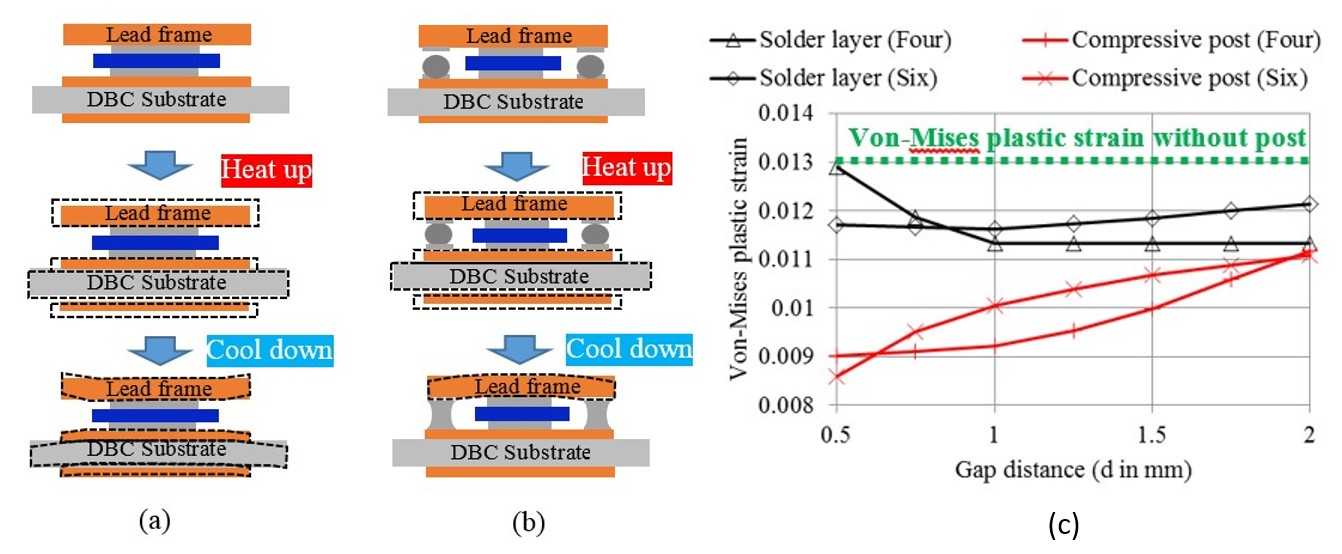
Fig. 1. Deformation (dashed line) in double-sided module (a) without and (b) with compressive posts; (c) Simulated Von-Mises plastic strains at the top solder layer and compressive post.
A double-sided module exhibits electrical and thermal characteristics that are superior to their wire-bonded counterpart. Such structure, however, induces more than twice the thermo-mechanical stress in a single-layer structure. Compressive posts have been developed and integrated into the double-sided module to reduce the stress to a level acceptable by silicon dice. For a 14 mm 21 mm module carrying 6.6 mm 6.6 mm die, a finite-element simulation suggested an optimal design having four posts located 1 mm from the die; the z-direction stress at the chip was reduced from 17 MPa to 0.6 MPa.
For the 6.6 mm 6.6 mm die studied, the optimal arrangement would place four posts symmetrically around the chip, each post at a distance between 0.75 mm and 1 mm from the chip's edges. The bonded chips no longer detached, and the module fully functioned after being sandwiched between a DBC substrate and a copper lead frame. The Von-Mises plastic strain at the die-attach layer was reduced to 87.69% of the strain without compressive posts, implying enhanced fatigue for the lifetime of the joint.
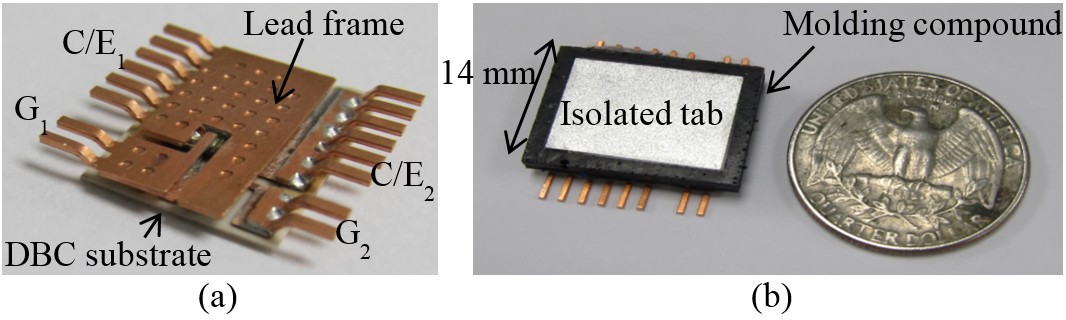
Fig. 2. Developed double-sided module with compressive posts before (a) and after (b) encapsulation.