LIBRARY
A Power Hardware-in-the-Loop Testbench for Aerospace Applications
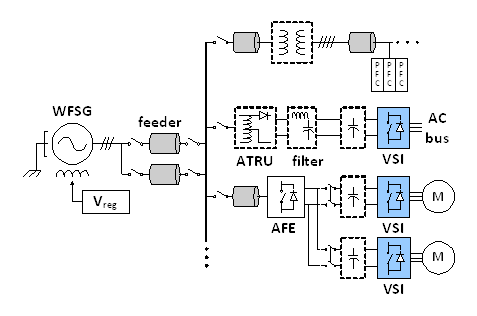
This work centers around the demonstration of the various capabilities of EGSTON Power Electronics COMPISO System Unit CSU200-1GAMP6 (CSU) P-HIL platform. An advantage of this platform is the four-quadrant power amplifiers that allow the unit to act as a voltage or current source or load. Two of the key results demonstrate the capabilities of the CSU to emulate power converters and electric machines. The diode rectifier is modeled using a switching function approach and assuming ideal switches. Additionally, the synchronous generator is modeled using the fifth-order model with a damping winding on the D and Q axes. The induction motor is modeled using the traditional DQ approach as well. Fig. 2 shows the CSU accurately emulating an induction machine.
This paper presents the capabilities of the CSU to emulate electric machines and power electronics through a series of tests. The electric machine emulation is validated through comparison with real-world test results, and the power electronics emulation test cases are validated though comparison with simulation results.
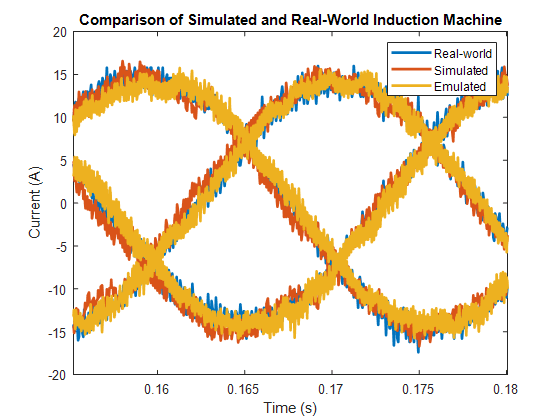