RESEARCH
Hybrid CM and DM Inductor Design for EMI Filter
A large grounding impedance of the filter will degrade the desired attenuation profile. Symmetry in the filter topology and careful placement of the filter (to reduce the ground path in the system) accounted for 30 dB increased attenuation as compared to an asymmetric topology and placing the filter 15 cm further from the system. This allowed for the use of smaller components to provide the same attenuation to the original system. In order to optimally utilize the volume of a magnetic core and windings the DM and CM inductors are integrated into one structure sharing their windings.
Careful design of the EMI filter will minimize the size and weight of the filter and the overall system. This design procedure is validated for DC-fed motor drives but is applicable for the majority of power conversion systems where size and weight is of concern; for example, aircraft, shipboard, and vehicular applications.
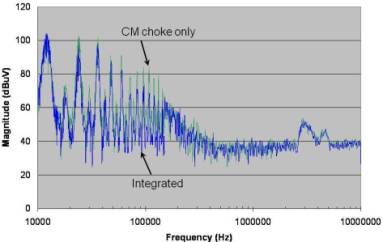
hybrid CM and DM inductors (blue).