RESEARCH
Thermomechanical Reliability of Nanoscale Silver Paste for Large-Area Device Attachment
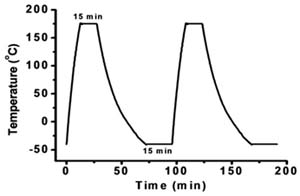
We explored a strategy of using nanoscale metal particles to forming the attachment by a low-temperature sintering technique. This approach utilizes the large thermodynamic driving force for densification. Based on the science of sintering, the driving force for densification of a particle compact increases with decreasing particle size due to increasing surface area to volume ratio and particle surface curvature. Thus the densification rate, a product of thermodynamic driving force and kinetics of a nanoparticle compact can still be high at low temperatures despite low atomic diffusion coefficients at low temperatures.
This study focuses on evaluating the high-temperature reliability of nanoscale silver paste for large-area device attachment by means of passive temperature cycling, from -40°C to 175°C, as shown in Fig. 1. Parametric study firstly determines the type of the silver paste, processing profile, and the pressure applied during the sintering stage. Thermomechanical reliability of samples attached with nanoscale silver paste showed different failure mode from the samples attached with other high-temperature die-attach material, AuSn and AuGe solder alloys, shown in Fig. 2. Due to the low elastic modulus of the sintered joint, 9 GPa, thermomechanical stress generated between semiconductor chip and copper substrate is much smaller than samples bonded with solder alloys.

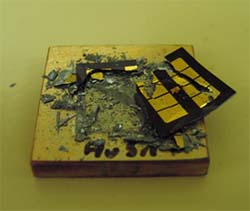
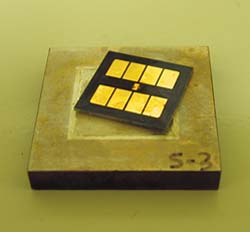