RESEARCH
Medium Voltage AC to 400V DC Rectifier for Data Center
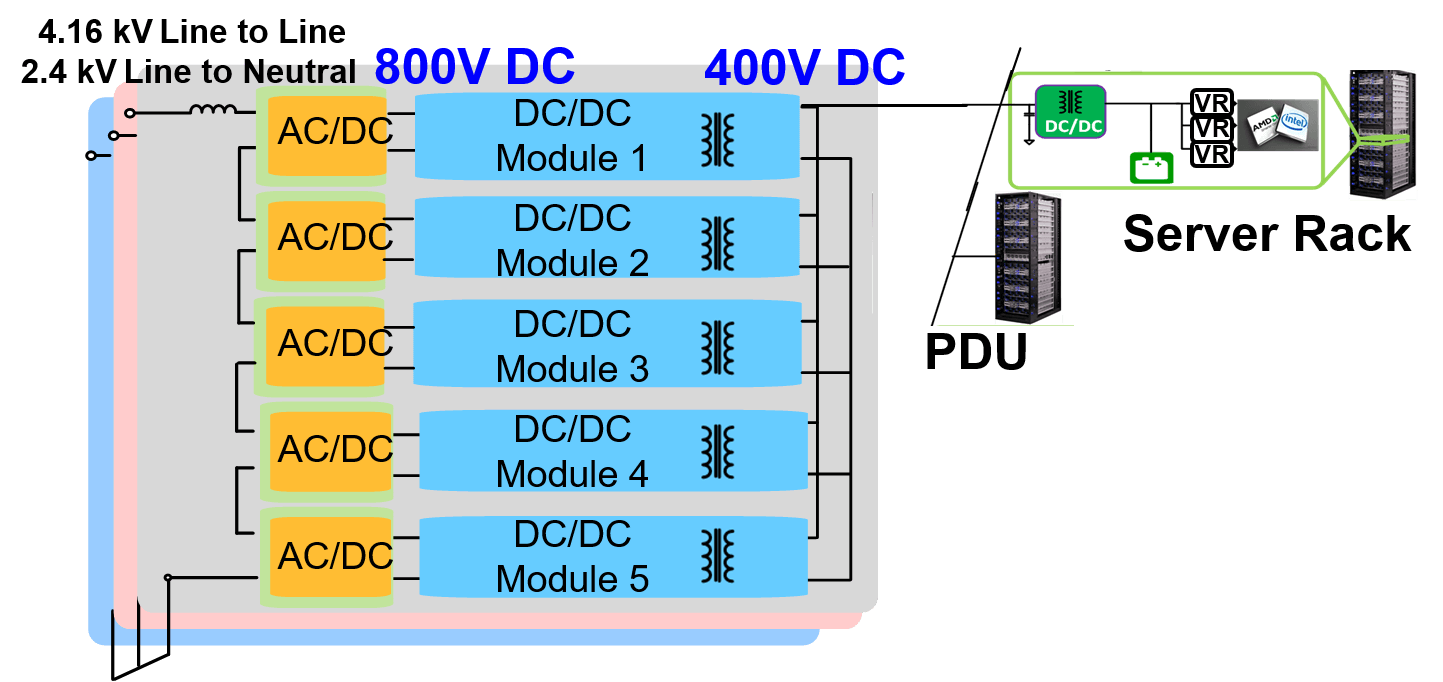
In this work, a high-frequency, high-efficiency isolated CLLC resonant converter is proposed for a next generation dc data center. The medium-voltage, high-frequency transformer is the most crucial component in terms of insulation and power density. A novel UU core with sectionalized winding structure is chosen to enhance insulation capability, restrict leakage inductance, and reduce magnetic loss at the same time. Transformer insulation parameters are calculated based on the IEEE Std. C57.12.01 requirements. An additional conductive shielding layer is applied to restrain the electric field inside the insulation and make sure there is no electric field in the air. A stress-grading layer is utilized at termination to spread out equal potential lines and thus reduce the E-field around termination. The winding arrangement is optimized based on the smallest insulation volume.
The transformer turns number is based on the transformer loss volume trade-off and the core loss winding loss trade-off. The impact of a different working frequency and different core loss density on transformer design is also analyzed based on a similar method. 200 kHz is found to be the best working frequency for ML27D material from Hitachi in this application. A 15 kW/200 kHz converter prototype is developed as shown in Fig. 2. Experimental results are also presented with 98.7% peak efficiency and 61 W/in3 power density.
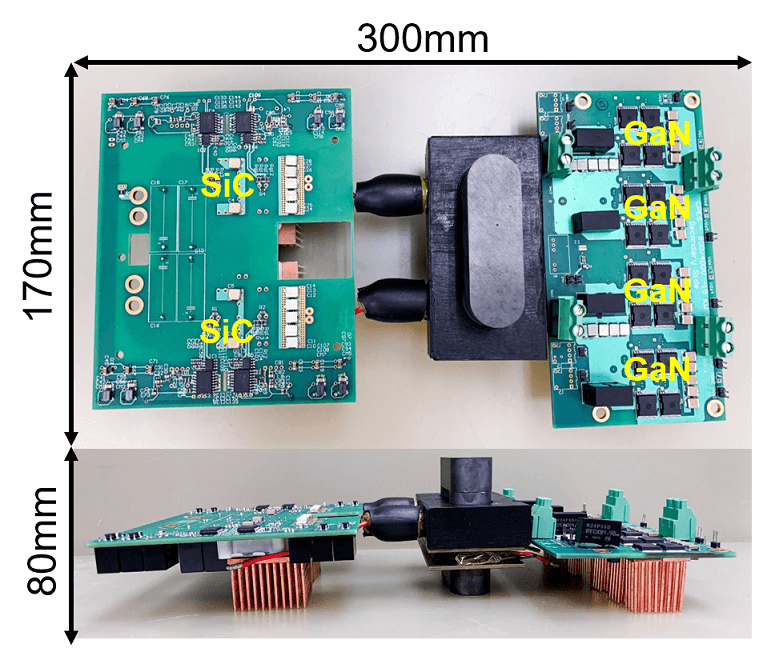