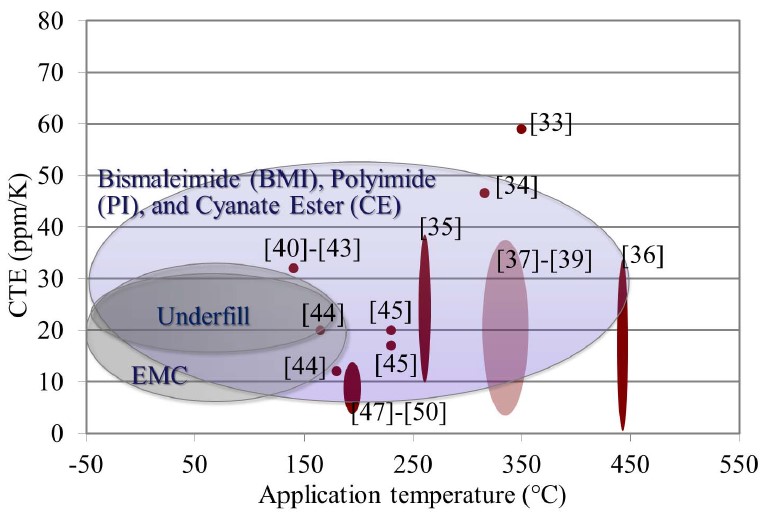
Fig. 1. CTE and maximum operation temperature of commercial underfills and molding compounds.
Semiconductor encapsulation is crucial to electronic packaging because it provides protection against mechanical stress, electrical breakdown, chemical erosions, radiations, and so on. Conventional encapsulants are only applicable below 150 °C. However, with increasing demand for high-density and high-temperature packaging, encapsulants that are functional at or above 250 °C are required. In this paper, five types of encapsulants, including conformal coatings, underfills, molding compounds, potting compounds, and glob tops, are surveyed. First, recommended properties and selection criteria of each type of encapsulant are listed. Second, standard test methods for several crucial properties, including glass-transition temperature (Tg), coefficient of thermal expansion (CTE), dielectric strength, and so on are reviewed. Afterward, commercial products with highoperation temperature are surveyed. However, the results of the survey reveal a lack of high-temperature encapsulants. Therefore, this paper reviews recent progress in achieving encapsulants with both high-temperature capability and satisfactory properties. Material compositions other than epoxy, such as polyimide (PI), bismaleimide (BMI), and cyanate ester (CE), are potential encapsulants for high-temperature (250 °C) operation, although their CTE needs to be tailored to limit internal stress. Fillers are reported to be efficient in reducing the CTE. In addition, fillers may also have a beneficial impact on the thermal stability of silicone-based encapsulants, whose high-temperature capability is limited by their thermal instability.
Recent literature is surveyed for possible methods to develop encapsulants with both high-temperature capability and acceptable properties for semiconductor packaging. For epoxy-based materials without high Tg, rigid structures (naphthalene, fluorene, etc.) can be formulated into their chemical structure to increase Tg. For high-Tg materials with high CTE, various fillers (silica, Al2O3, ZrW2O4, etc.) can be formulated into polymer matrix to reduce CTE. Fillers may also help to increase the thermal stability of silicone-based potting compounds by restraining the chain mobility and increasing crosslink density.
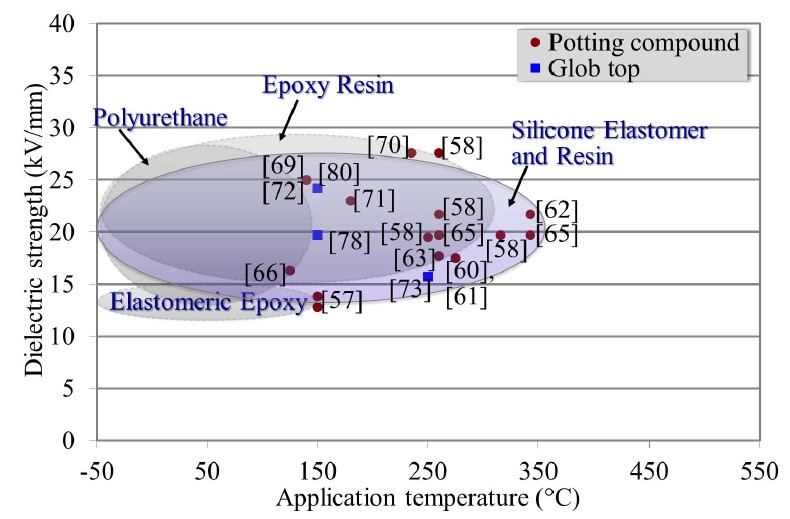
Fig. 2. Dielectric strength and maximum operation temperature of potting compounds and glob tops.