LIBRARY
Shipboard PEBB Cooling Strategies
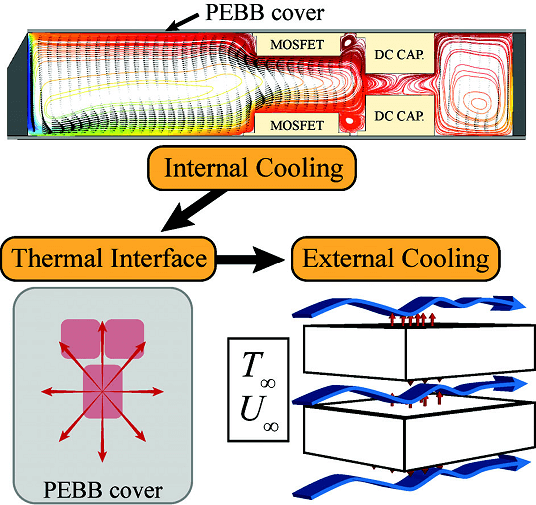
The thermal management of PEBBs can be divided into three aspects, as shown in Fig. 1: internal cooling, thermal interface (PEBB envelope), and external cooling. The internal cooling ensures proper heat dissipation from the local heat sources (e.g., MOSFET) to the thermal interface via diffusion and natural convection. Similarly, the thermal interface plays a key role in providing necessary heat flow paths from the PEBB interior to its exterior for an even heat distribution and increased heat transfer to the external cooling medium. The external cooling of PEBBs is typically achieved with forced air or liquid while more sophisticated methods such as heat pipes and microchannels may be employed to spread heat to a bigger area.
The advantages and disadvantages of several options for external cooling of PEBB units are explored, including air cooling, single-phase liquid cooling, external liquid cooling with a dry interface and other advanced methods. Based on calculation and simulation results like the one shown in Fig. 2, the proper cooling options can be determined based on the loss requirements and other thermo-mechanical considerations. Per the results, preliminary numerical simulations indicate that air cooling is likely to be sufficient to meet the cooling needs of the PEBB 1000, as long as the internal heat sources are placed in direct contact with the thermal interfaces followed by optimized heat-sink-finned structures. For the higher voltage/power PEBB units, air cooling, water cooling, and water cooling with a dry interface all have potential for meeting the cooling needs and war- rant further investigation. In any case, the localized heat generated within the PEBB will require spreading to a larger surface area for subsequent transfer out of the PEBB. Having identified potential cooling strategies for PEBB 1000 and PEBB 6000, future work should include additional analysis to determine efficacy, efficiency, size and weight of the possible methods.
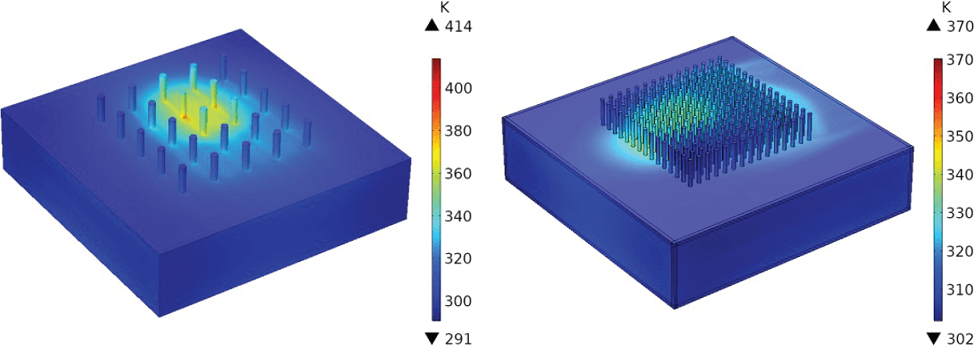