LIBRARY
Electrical Insulation Design and Qualification of a SiC-based Generator-Rectifier Unit (GRU) for High-Altitude Operation
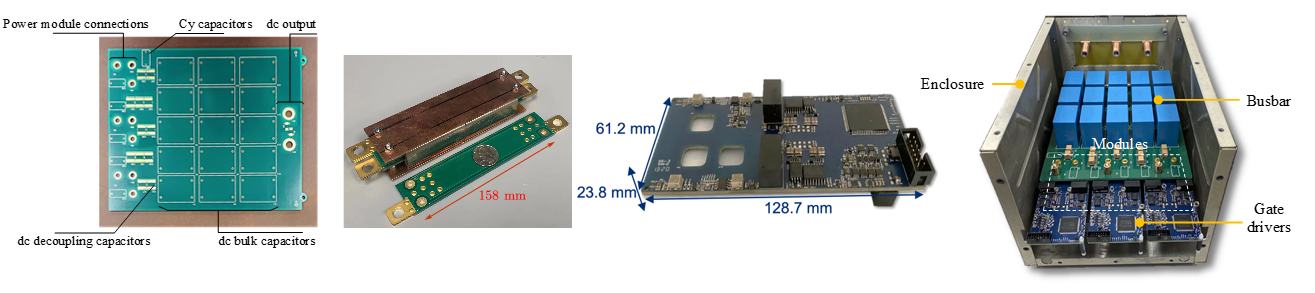
Printed circuit boards (PCBs) are ideal for integration of electronic components in low profile, high power density assemblies where precise E-field control techniques can be easily imple-mented to achieve sufficient PD performance even under the specified altitude conditions. With the knowledge of the Paschens curves for air, it is possible to deduce the breakdown E-field of air for varying conductor clearances at different altitude conditions to directly guide the GRU design.
In this work, the GRU in question is designed and qualified for PD free operation at 15,200 m altitude (11.6 kPa). Finite element analysis simulations are used to optimize the design of the GRU PCBs and their assemblies to constrain the surface E-field (Eair in air) of the system under a predetermined limit (Eair-limit ⩽ 300 V/mm) chosen based on the Paschen curves to eliminate PD occurrences under nominal conditions. The three main GRU component assemblies, the dc bus, the CM choke, and the gate driver, are shown in Fig. 1. A high altitude PD test bed was designed for GRU insulation qualification (Fig. 2 (a)) and PD experimental results of individual GRU com-ponents and their assemblies are presented in Fig. 2(b) showing satisfactory PDIV values (> 1.4 times the working voltage) at the specified air pressure conditions.
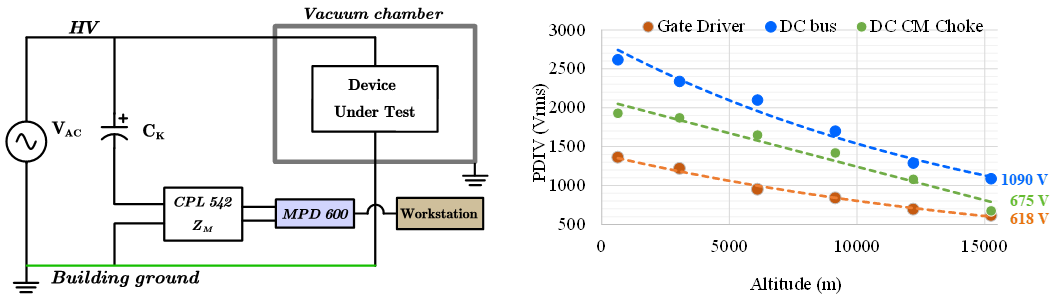