LIBRARY
Effects of Underfill Properties on the Thermo-Mechanical Reliability of Double-Side Cooled (DSC) Power Modules
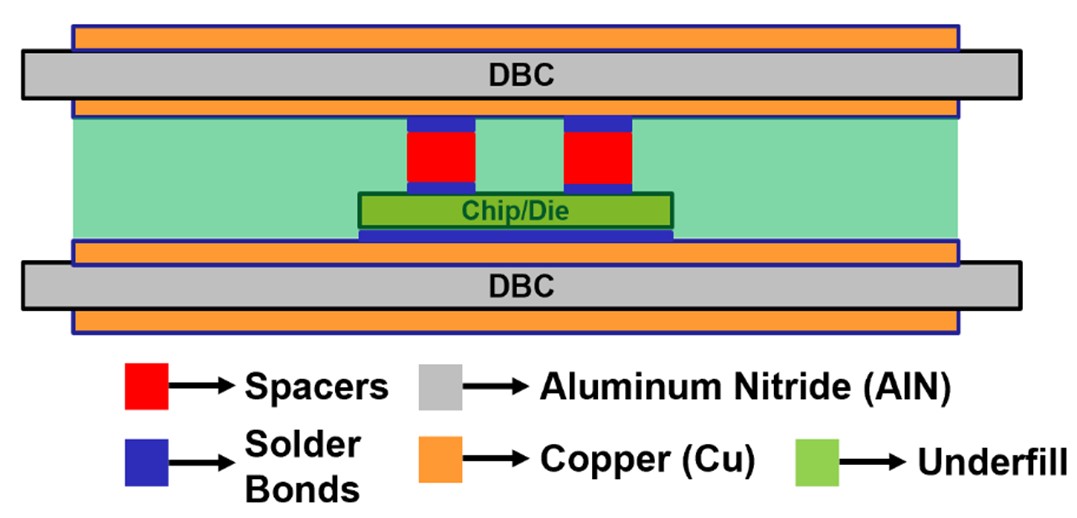
This work aims to gain a better understanding on the thermomechanical reliability of DSC power modules. More specifically, it focuses on understanding the effects of various material properties of the encapsulation or underfill, used for packaging the devices, on the module reliability.
A series of finite element analysis (FEA) simulations are designed to investigate the thermo-mechanically induced stresses and strains inside a typical DSC package modeled in Fig. 1. The model package consists of two parallel direct-bonded copper (DBC) substrates, one device bonded on one substrate, two metal posts connecting the device to the other substrate, and an underfill filling the empty space in between. The package is assumed to undergo accelerated tests, such as temperature-cycling and power-cycling. Isotropic elastic and isotropic viscoelastic (such as Anand) models are used to describe the mechanical behaviors of the materials.
Anticipated results of the FEA simulations will help to elucidate: (1) the locations where inside the package the thermal stresses and strains are concentrated; (2) effects of underfill on those stresses and strains; and (3) which material property or properties of the underfill is or are more effective for improving the reliability of the module.