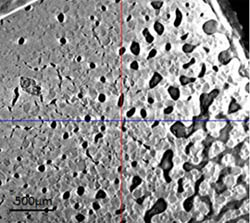
Fig. 1. X-ray reconstructed image of sintered micron-sized silver laye r in a commercial module, which shows the initial silver particles in the micrometer scale and significant numbers of voids and cracks are present in significant numbers.
Low-temperature joining with sintered silver is being developed as a lead-free, non-solder die-attach solution for packaging power devices and modules. The advantages of using silver include superior thermal and electric conductivities, high ductility and high operating temperature. While its feasibility has been demonstrated, one major drawback of sintered silver joint is the high applied pressure during sintering to produce the desired bond strength. A high percentage of voids could also remain in the sintered joints. Applying the technique to large-area attachments also means a correspondingly higher applied force and damage to the devices and substrates is not far-fetched.
This study focused on the use of nanoscale silver paste as the attachment material, which can be sintered at relatively low temperature and pressure. Contrast to the traditional press-aided sintering, an improved attachment technique is carried out, which can lower the temperature and time during the hot-press stage. With 3MPa pressure at 180°C for 5 minutes, the assembly can then sinter at 275°C without pressure. Test results on the attached samples showed that no detectable voids or cracks were found in the sintered silver layer and the device appeared to be strongly bonded when a measurable curvature was obtained.
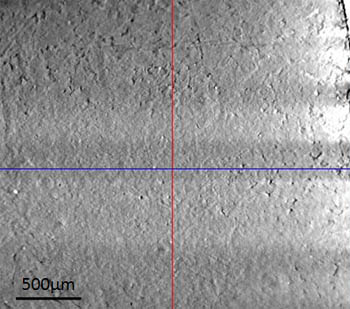
Fig. 2. Reconstructed x-ray image of the sintered nanoscale silver paste layer, which is generally uniform with only a few tiny cracks and pinholes possibly present.