LIBRARY
Fabrication of a Double-side Cooled, High Temperature Power Module with Sintered Nanosilver Interconnect for Automotive Applications
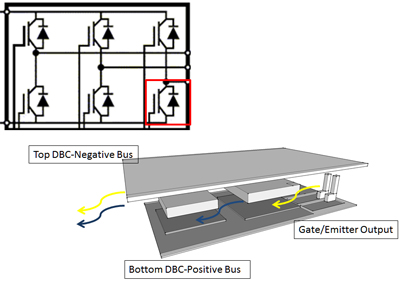
Solder alloys generally have low electrical and thermal conductivity, and are unreliable when cyclic loaded. As operating temperatures approach melting points joint reliability worsens. By utilizing the emerging low-temperature joining technology (LTJT), which is based on the sintering of silver powders, the die interconnect thermal and electrical properties can be enhanced. In addition, several leading European manufacturers of power modules have demonstrated a significantly improved performance and reliability of power modules interconnected by the LTJT technology over the soldering technology. However, a barrier for implementing the technology has been the requirement of pressure, 10 to 40 MPa or 100 to 400 kg-force on a 100 mm2 chip, to lower the silver sintering temperature from over 700°C down to about 250°C. This limits production throughput, complicates the manufacturing process, and places critical demands on substrate flatness and thickness of the chips.
For this research we utilize a newly designed nanosilver paste that can be sintered with zero or pressure less than 5 MPa for speeding up the LTJT implementation. Reduction of pressure coupled with the lower sintering temperatures allows for the manufacture of more intricate geometries. In this study, we focused on making a quarter-bridge module consisting of one IGBT in parallel with one diode. Module schematics of the proposed quarter bridge circuit utilizing a top and bottom DBC substrate can be seen in Figure 1. The quarter bridge circuit can easily be combined with other units for a full inverter package and the double-side design is ideal for integration and thermal management. In this paper, we report the use of this enabling nanomaterial for successful fabrication of planar, double-side cooled quarter bridge power modules.