
Fig. 1. Interleaved 2L VSI DC-fed motor drive system.
An adjustable-speed motor drive with a voltage-source pulse-width modulation inverter with long cables (shown as Fig.1) brings the EMI issues to the motor drive system [1]. Usually EMI filters are part of the system that makes both AC and DC sides meet the EMI requirement (such as DO160E standard), which takes a large portion of the system weight. To improve system power density and reliability, a paralleled and interleaved converter topology is commonly used. By phase-shifting the PWM switching cycles of individual converters with an appropriate angle, the total voltage ripple due at PWM switching at the ac terminal can be reduced, which provides the possibility of EMI filter weight reduction. To reduce EMI filter weight, a small angle interleaving is presented in the previous study, which shows the reduction on inductor values (as shown in Fig.2). However, in inductor design, inductor weight is also related with the volt-second on the inductor (as shown in Fig.3) where symmetrical interleaving has a higher benefit.
Considering the noise propagation path impedance and volt-second on the induc-tors, the selection of the interleaving angle is analyzed in detail in order to study the impact of interleaving on the real EMI filter weight reduction. Different interleaving angles are compared for both the AC and DC side of the EMI filter design. This shows that symmetric interleaving gives a smaller EMI filter weight for the AC side, however a small angle interleaving is better for DC side (as shown in Fig.4).
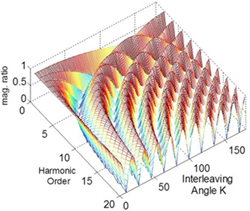
Fig. 2. Voltage reduction ratio on different order harmonics with different κ.
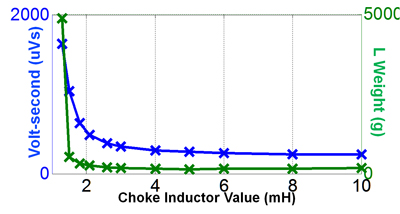
Fig. 3. Filter weight: green and volt-second blue: VS inductor value.
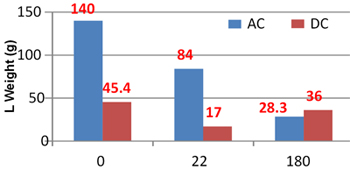
Fig. 4. AC and DC side EMI filter weight comparison with different interleaving angle.