LIBRARY
15 kW Step-up Mode SiC Matrix Converter Design with 3D Commutation-loop Layout and PCB Aluminum Nitride Cooling Inlay
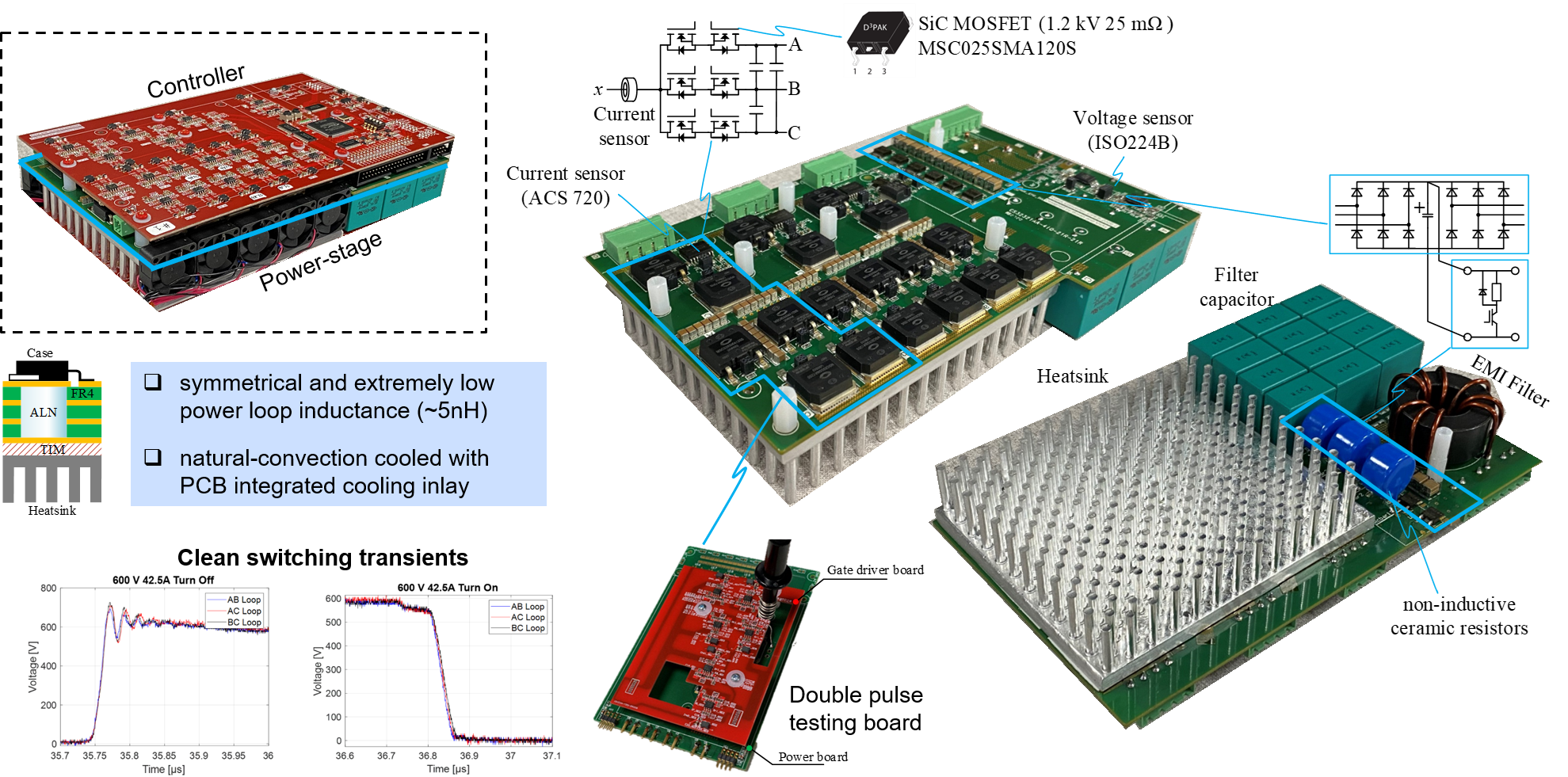
First, as a key component of MxC, bidirectional device configuration is selected based on the trade-off between digital controller and powerline electromagnetic emissions. It is found that the common-source configuration for the bidirectional switch exhibits reduced noise emission at the controller side while the common-drain configuration benefits the power-line noise reduction. Second, as surface- mount device features low manufacturing cost, compact package, and low stray inductance, surface-mount instead of through-hole SiC MOSFETs are adopted. To solve the concern on the heat dissipation, a thorough evaluation on surface-mount device cooling approaches is provided. Thermal via, metal-core PCB and aluminum nitride inlay cooling approaches are considered. The PCB aluminum nitride cooling inlay stands out to be an effective cooling approach which can handle high per-device loss (24 W) with very limited impact on PCB layout flexibility. 3D vertical commutation-loop methodology is then employed to achieve small and symmetrical loop inductance for the 3 coupled commutation loops in a MxC phase-leg. Clean and symmetrical switching transient test results are provided to verify the 3D loop design. A highly integrated 15 kW MxC prototype is eventually demonstrated with a power density of 15 kW/L and 20 kW/kg, as shown in Fig. 1. The prototype exhibits a full-load efficiency of 99.0% and is compliant with DO-160G standard. The CCM operation is experimentally verified on the prototype where the 380 V generator voltage is boosted by the MxC to establish a 480 V three-phase ac bus, as shown in Fig. 2.
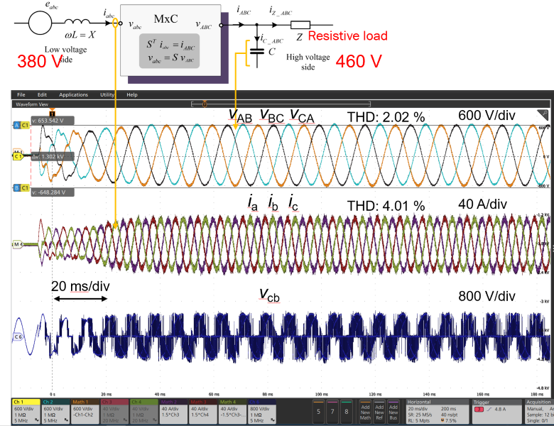